在工程设计与制造领域,材料利用率与结构性能的平衡始终是核心挑战。随着计算力学与人工智能的深度结合,基于拓扑优化算法的CAD软件正在重塑产品开发范式。这类工具通过数学建模自动推导出满足力学性能的最优材料分布方案,使工程师能够突破传统经验主义设计框架。空客A350机翼支撑结构通过Altair OptiStruct实现减重15%的同时提升承载能力,印证了这种技术革新带来的商业价值。
1、技术原理突破
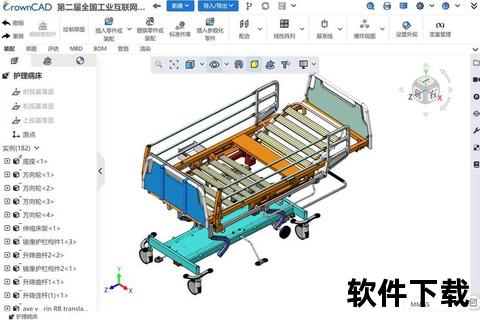
拓扑优化的数学本质是求解材料在给定设计域内的最优分布问题。基于变密度法的连续体拓扑优化,通过有限元网格将设计域离散化,每个单元用密度参数表征材料存在概率。Bendsoe和Sigmund提出的SIMP(Solid Isotropic Material with Penalization)模型,通过引入惩罚因子迫使中间密度值趋向0或1,有效解决了棋盘格现象等数值不稳定问题。
现代算法融合了机器学习技术,ANSYS Discovery通过神经网络预测初始设计空间,将优化迭代次数降低40%。浙江大学团队开发的并行优化框架,利用GPU加速技术将百万单元规模问题的求解时间从72小时压缩至3.5小时。这些突破使得拓扑优化从实验室走向工程实践,西门子NX 12.0已将实时拓扑优化模块集成到设计流程中。
2、多学科应用拓展
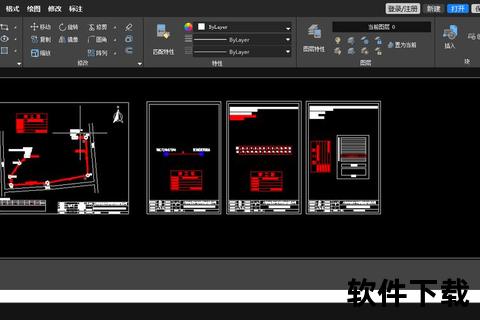
在航空航天领域,波音787机身隔框采用拓扑优化设计后,不仅实现28%的减重效果,其振动模态特性还满足了严苛的适航标准。洛克希德·马丁公司应用GENESIS软件优化卫星支架结构,在太空辐射环境下仍保持结构完整性。这类应用证明,软件能够同时处理静态强度、动态特性等多目标约束。
生物医疗领域正在发生革命性变化。西安交通大学团队利用3-matic软件设计的人工髋关节,通过仿生多孔结构使骨细胞长入速度提升60%。MIT研究人员开发的个性化手术导板,结合患者CT数据与拓扑优化算法,将手术精度控制在0.2mm以内。这些案例显示,软件正突破传统制造限制,开创个性化医疗新纪元。
3、经济价值重构
汽车行业的数据最具说服力:福特汽车应用OptiStruct优化底盘部件,单车型年度材料成本降低230万美元。更值得关注的是,软件驱动的设计变革正在重塑供应链结构。特斯拉一体化压铸车身设计,通过拓扑优化将70个零件整合为1个,使生产线占地面积缩减40%。这种集成化设计不仅降低制造成本,更重构了传统汽车制造的价值链。
建筑领域的革新同样显著。扎哈·哈迪德建筑事务所应用ParaCloud工具设计的北京大兴机场屋顶结构,用钢量比传统方案减少35%,同时满足9度抗震要求。这种高效设计使项目总造价降低8.2%,验证了拓扑优化在大型工程项目中的经济可行性。Arup公司的研究表明,建筑结构优化可使全生命周期碳排放降低12%-18%。
4、技术挑战解析
算法复杂度仍是主要瓶颈。当处理非线性、多物理场耦合问题时,传统梯度优化法的收敛速度呈指数级下降。宾夕法尼亚大学研究显示,在涉及热-力耦合的电子器件散热优化中,计算耗时比单物理场问题增加7-9倍。对此,Altair开发的morphing技术通过设计空间缩减,将设计变量从10^5量级压缩至10^3,显著提升计算效率。
制造约束的数字化表达是另一难题。增材制造允许的悬垂角度、传统加工的最小特征尺寸等限制,需要转化为数学约束条件。达索系统在CATIA中引入制造可行性模块,通过几何推理算法自动修正违反工艺约束的设计特征。慕尼黑工业大学开发的约束传播算法,能实时检测并修正不可制造结构,使设计首次通过率提升至83%。
站在智能制造的时代节点,拓扑优化CAD软件已从辅助工具演变为创新引擎。它打破了经验驱动的传统设计模式,通过算法发掘出超越人类直觉的优化方案。随着数字孪生、量子计算等技术的融合,未来的设计软件或将实现实时多目标优化,在纳米级精度与城市级尺度间自由切换。建议研究机构加强跨学科人才培养,推动算法开发与工程实践的深度耦合,同时建立覆盖全产业链的优化设计标准体系。唯有如此,才能充分释放这项技术的变革潜力,助力中国制造向中国创造的历史性跨越。