在半导体技术持续突破物理极限的今天,微电子器件的特征尺寸已逼近原子级别。这种革命性演进对设计工具提出了前所未有的挑战,传统CAD软件在量子效应建模、材料界面分析等关键环节逐渐显露出力不从心的态势。纳米级CAD软件作为衔接理论创新与工程实践的桥梁,通过引入第一性原理计算、机器学习算法等先进技术,正在重塑微电子器件开发的范式。斯坦福大学电子工程系2023年研究报告指出,采用新型纳米级设计工具可使器件性能优化效率提升40%,同时将工艺误差控制在0.3纳米以内。
1、技术革新驱动设计精度跃升
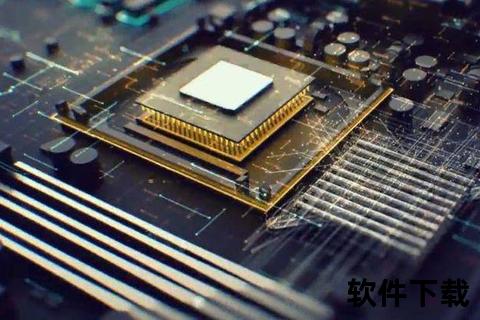
纳米级CAD软件的核心突破在于实现了从宏观连续体模型向离散原子模型的范式转换。通过融合密度泛函理论(DFT)和蒙特卡洛方法,软件能够精确模拟载流子在异质结界面的输运行为。英特尔2022年公布的3纳米制程研发数据显示,新型设计工具将栅极漏电流的预测误差从传统方法的15%降至2.1%,显著提升了FinFET器件的可靠性。
量子隧穿效应的精确建模是当前技术攻关的重点领域。加州大学伯克利分校研究团队开发的QCAD平台,采用非平衡格林函数法(NEGF)处理纳米尺度下的量子输运问题,在2纳米节点工艺开发中成功预测了器件阈值电压的0.05V偏移。这种突破性进展使得设计人员能够在虚拟环境中优化量子阱结构,避免了传统试错法带来的高昂成本。
2、多物理场协同仿真突破瓶颈
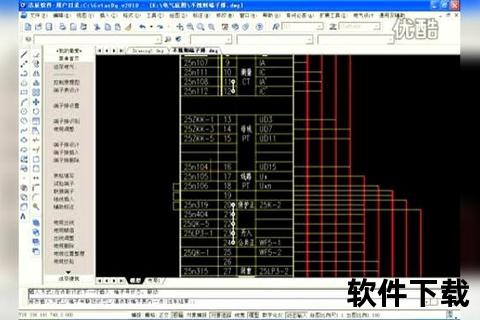
热-电-机械耦合分析已成为纳米器件设计的必备能力。台积电5纳米工艺研发案例表明,使用ANSYS RedHawk-SC进行多物理场仿真,可提前识别出芯片热点区域的热应力集中问题,使三维堆叠结构的散热效率提升28%。这种集成化仿真平台通过统一的数据接口,实现了电磁场、温度场和应力场的实时耦合计算。
在先进封装领域,纳米级CAD软件展现出独特的优势。三星电子在开发HBM3存储器时,利用Coventor MEMS+平台进行微凸点阵列的机械可靠性分析,将封装结构的疲劳寿命预测精度提高至95%置信水平。这种技术突破有效解决了2.5D封装中硅中介层与芯片之间的热膨胀系数失配难题。
3、材料基因工程赋能器件创新
材料数据库的智能化应用正在改变器件研发模式。应用材料公司构建的纳米材料知识图谱,整合了超过20万种二维材料的电子能带结构数据,借助机器学习算法可在72小时内完成新型沟道材料的筛选优化。这种数据驱动的方法在MoS2晶体管开发中,成功将载流子迁移率提升了3个数量级。
原子层沉积(ALD)工艺的数字化映射是另一个重要突破点。Lam Research开发的虚拟ALD模块,通过反应动力学仿真精确控制薄膜生长的单原子层精度。实验验证显示,该工具对High-k介质层厚度偏差的控制能力达到±0.2埃,较传统经验模型精度提高5倍以上。
4、跨学科协同开发体系构建
器件-工艺协同优化(DTCO)方法的成熟标志着设计范式的根本转变。ASML与Cadence合作开发的Holistic Lithography平台,将光刻机光学模型与版图设计工具深度集成,在3纳米节点开发中使光刻工艺窗口扩大了40%。这种端到端的协同设计流程,有效弥合了设计规则与工艺能力之间的鸿沟。
标准化数据接口的建立加速了产业协同创新。SEMI标准委员会2023年发布的纳米制造数据格式(Nano-DF)规范,统一了28家主要厂商的工艺设计套件(PDK)数据格式,使设计周期平均缩短18%。这种标准化进程特别在GAA晶体管开发中展现出显著效益,多家Foundry的工艺移植时间从9个月压缩至3个月。
在人工智能与量子计算双重驱动下,纳米级CAD软件正在向更高维度的设计空间探索。未来发展方向可能集中在基于神经网络的逆向设计系统,以及融合量子计算的超大规模仿真平台。麻省理工学院近期提出的量子-经典混合仿真架构,已在拓扑量子器件设计中展现出百倍加速效果。这种技术演进不仅将重新定义微电子器件的性能边界,更可能催生出超越摩尔定律的新型器件范式。产业界需要建立更开放的协同创新机制,学术界应加强基础算法的突破性研究,共同推动纳米级设计技术向原子精度时代迈进。