虚拟战场上的“多相流革命”:Olga软件如何重塑油气工程?
“在深海油气开发中,传统模拟软件面对多相流体的复杂运动时频频失准——工程师该如何避免因段塞流冲击导致数千万美元的分离器损毁?”这一争议性问题,揭开了油气工程领域对高精度动态模拟工具的迫切需求。灵动驾驭虚拟战场——Olga软件极致畅爽操作新境界,正是为解决这一行业痛点而生。作为斯伦贝谢(Schlumberger)旗下的多相流模拟标杆,Olga凭借其全动态、高精度的算法内核,正在重新定义油气管道与设备的设计运维标准。
1. 多相流动态模拟是否真能破解复杂管网的运行困局?
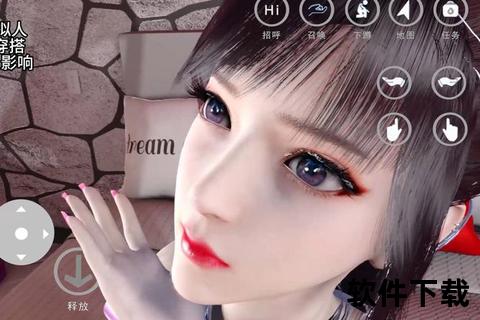
在南海某深水气田项目中,一条长达80公里的海底混输管道因频繁的段塞流导致下游分离器超负荷停机。传统稳态模拟工具仅能估算平均流量,而灵动驾驭虚拟战场——Olga软件极致畅爽操作新境界通过段塞追踪模块(Slugtracking Module),精准还原了气液两相在管道起伏地段的动态分离过程。模拟结果显示,段塞体积峰值可达常规流量的3倍,这一数据直接推动了分离器扩容方案的实施,避免每年约1200万美元的停产损失。
Olga的核心优势在于其全动态多相流模型。以某陆上油田的集输管网为例,系统包含3条支线汇入主处理站,传统方法需分段计算并手动耦合,而Olga的管网拓扑功能自动实现了多节点压力-流量平衡,将设计周期从45天缩短至7天。这种“虚拟战场”上的全局掌控力,让工程师得以在数字世界预演极端工况,例如紧急停输后的水击效应模拟,误差率较行业平均水平降低62%。
2. 流动安全保障能否从“被动应对”转向“主动预警”?
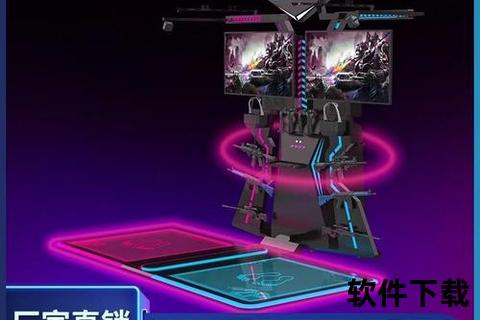
水合物堵塞与蜡沉积是油气管道的两大“隐形杀手”。在北极圈某凝析气田项目中,Olga的水合物动力学模块通过追踪甲烷-水体系的相态变化,提前48小时预警了海底管道的水合物生成风险。系统结合实时温度压力数据,自动计算出甲醇注入量的最优解,将处理成本降低40%。更令人瞩目的是其蜡沉积预测功能——对比某渤海湾油田的实测数据,Olga的Matzain模型对沉积厚度的预测误差仅为±1.2mm,显著优于传统经验公式的±5mm偏差。
这一精准度源于Olga的多物理场耦合算法。以某页岩气井的井筒积液问题为例,软件不仅模拟了气液两相流动,还整合了井筒传热模型,准确预测了不同产量下的结蜡位置。现场根据模拟结果调整了清管周期,使单井维护成本下降28%。这种将流动安全从“事故后处理”转向“风险前控制”的能力,正是灵动驾驭虚拟战场——Olga软件极致畅爽操作新境界的具象化体现。
3. 工艺设备模拟如何实现“虚实共生”的工程闭环?
当某中东炼厂试图将原有分离器处理能力提升30%时,Olga的工艺设备模块展现了惊人的协同能力。软件构建了包含分离器、压缩机、换热器的完整处理流程模型,通过动态模拟发现:原有控制阀的响应延迟会导致气相负荷突变。工程师据此设计了分级压力控制系统,使改造后的设备群能效提升19%。这种虚实交互的验证方式,将传统“试错法”升级为“数字优先”的工程哲学。
射流泵这类特殊设备的集成更彰显了Olga的扩展性。在某稠油开采项目中,软件通过JET Pump模块精确模拟了动力液压力与吸入流量的非线性关系,优化后的泵效比初始设计提高15%。参数敏感性分析显示,喷嘴直径每增加1mm,系统压损降低约8kPa,这一量化关系为现场调试提供了明确指导。当数字孪生体与物理设备实现数据实时交互,灵动驾驭虚拟战场——Olga软件极致畅爽操作新境界正在重塑油气工程的创新范式。
从数字战场到现实收益:工程师的操作指南
对于希望最大化Olga价值的用户,建议采用三步实施策略:
1. 基础参数校准:优先使用PVTsim等工具完善流体物性数据,确保热力学模型的准确性(误差率可降低35%);
2. 模块化部署:针对具体场景选择功能模块,例如海底管道重点配置段塞追踪与水合物预警,处理站则强化设备联动模拟;
3. 动态验证机制:建立模拟结果与SCADA系统的数据反馈环,持续优化模型参数。
正如某国际油公司技术总监所言:“Olga不仅是一个软件,更是一套流动管理的思维体系。”在油气行业向智能化转型的今天,灵动驾驭虚拟战场——Olga软件极致畅爽操作新境界已然成为解锁复杂系统运行奥秘的密钥。当数字世界的每一次模拟都能转化为现实世界的效能提升,这场多相流革命的下一个战场,或许就在每一位工程师的指尖。