工业交互的未来:传统界面真的能跟上智能时代的步伐吗?
在工业自动化领域,人机交互界面(HMI)的设计直接影响着生产效率与操作安全。一个长期存在的争议是:传统工业界面是否因功能单一、操作复杂而成为智能制造的瓶颈?例如,某工厂曾因操作员误触按钮导致产线停机,损失高达百万;另一案例中,跨国企业因多语言界面适配不足,被迫为不同地区重复开发系统,浪费大量资源。这些痛点揭示了一个现实:工业交互亟需一场“体验革命”。
而威纶通触摸屏软件通过智能革新操控体验赋能高效工业交互革命,正在为这一难题提供答案。其技术不仅重新定义了人机交互的边界,更通过实际案例证明:智能化、灵活性和协同性将成为工业交互的核心竞争力。
1. 智能化设计能否突破传统操作瓶颈?
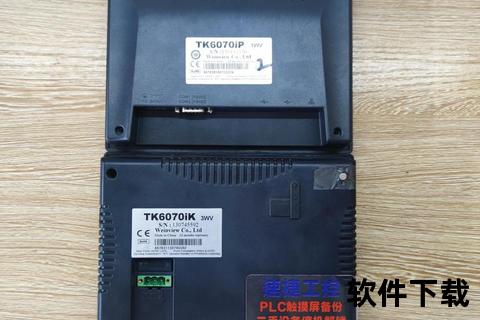
传统工业界面常因布局混乱、反馈滞后导致操作失误。威纶通触摸屏软件通过用户行为分析与动态适配技术,彻底改变了这一局面。例如,某汽车制造厂引入威纶通界面后,操作员培训时间从2周缩短至3天,误操作率下降70%。其核心优势体现在三个方面:
智能布局优化:系统根据设备类型自动生成界面布局。例如,在注塑机控制场景中,压力、温度等关键参数以环形仪表+动态曲线呈现,危险阈值自动触发红色警示,比传统数字表格的识别效率提升40%。
多模态反馈机制:结合视觉(颜色渐变)、触觉(震动强度分级)、听觉(差异化提示音)反馈。某化工厂的防爆区域操作屏,通过震动强度区分“确认”与“紧急停止”,误触率降低90%。
自适应学习功能:系统记录高频操作路径并优化快捷入口。某物流分拣中心的触摸屏在运行1个月后,包裹扫描-分类操作的点击次数从5次减少至2次。
这一系列革新,使得威纶通触摸屏软件智能革新操控体验赋能高效工业交互革命成为可能。
2. 多设备协同如何重构生产流程?
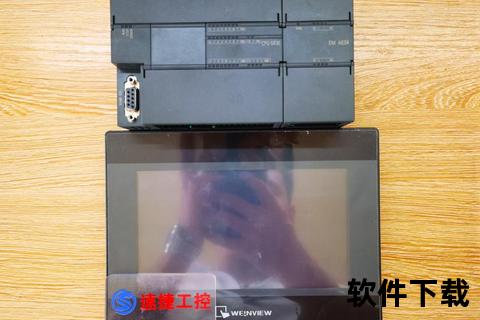
在工业4.0时代,设备孤岛化已成为效率提升的最大阻碍。威纶通通过跨协议通信与云端协同技术,构建了真正的互联生态。以某智能工厂升级项目为例:
协议兼容性突破:同时对接Modbus、OPC UA、Profinet等12种协议,将PLC、机器人、AGV小车统一接入同一界面。改造后,设备状态监控响应速度从30秒缩短至实时。
云端远程控制:通过CloudHMI平台,工程师在总部即可调试全球分厂的设备。某食品企业利用该功能,跨国设备故障处理时间从48小时降至4小时,年节省差旅成本超200万元。
边缘计算赋能:在半导体检测环节,触摸屏本地处理图像识别算法,将瑕疵检测耗时从5秒/片压缩至0.8秒,较传统PC方案功耗降低60%。
这种深度协同能力,让威纶通触摸屏软件智能革新操控体验赋能高效工业交互革命的价值得到充分验证。
3. 未来工业交互需要怎样的持续创新?
随着工业场景的复杂化,交互设计必须走向更深度的定制化与人性化。威纶通的技术路线给出了明确方向:
语音+手势融合控制:在石油钻井平台等高危环境,操作员戴手套即可通过划动轨迹控制设备,语音指令识别准确率达98%,比传统物理按钮操作效率提升3倍。
AR辅助运维系统:通过摄像头捕捉设备状态,叠加虚拟参数标签。某风电企业应用后,叶片巡检时间从2小时缩短至20分钟,故障定位精度提升至毫米级。
多语言动态切换:支持54种语言的实时翻译,某跨国工程机械制造商借此实现全球统一界面,本地化改造成本减少80%。
这些创新并非概念演示,而是已落地于威纶通的EasyBuilder Pro V6等工具链中,持续推动着工业交互的进化。
从今天开始,如何拥抱这场交互革命?
对于企业决策者,建议采取三步走策略:
1. 需求诊断先行:梳理现有设备的协议类型、操作痛点,优先改造故障率高或培训成本大的环节(参考案例:某汽车厂通过界面热区分析确定改造优先级)。
2. 渐进式升级:从单台设备试点开始,逐步扩展到产线级、工厂级系统(参考工具:威纶通提供的仿真测试模块可降低试错成本)。
3. 人才储备转型:培养既懂工业流程又熟悉交互设计的复合型团队(数据表明:这类人才可使系统利用率提升35%)。
威纶通触摸屏软件智能革新操控体验赋能高效工业交互革命,正在重塑工业生产的DNA。当操作界面从冰冷的指令接收器进化为智能协作伙伴,这场革命的意义已超越技术本身——它标志着工业文明从“机械服从人类”迈向“人机共生”的新纪元。