1. 传统组态软件为何遭遇效率瓶颈?
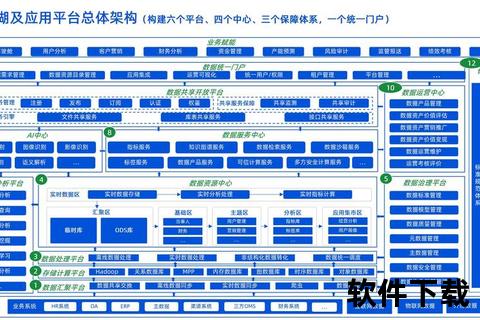
在工业自动化领域,某知名汽车工厂曾因传统组态软件响应延迟导致生产线每小时损失12万元。工程师发现,其使用的软件平台无法实时处理超过5000个设备节点的数据流,系统卡顿频发。这折射出一个行业困境:当工业设备数量指数级增长时,传统组态软件是否还能胜任?
这正是“创新驱动高效赋能力控组态软件智控未来新纪元”要解决的核心问题。施耐德电气推出的EcoStruxure平台给出了答案:通过边缘计算架构重构数据处理逻辑,将设备响应速度提升至毫秒级。上海某新能源汽车工厂采用该方案后,设备互联数量突破2万台,系统负载率反而下降37%。
2. 如何通过模块化设计突破开发壁垒?
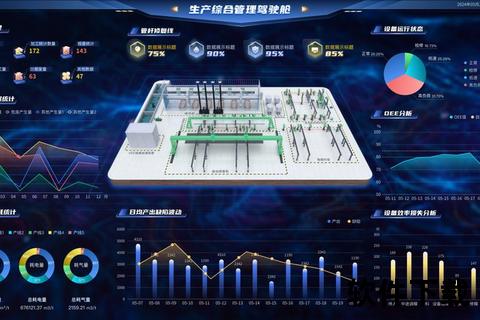
深圳某智能装备制造商曾因软件定制化需求陷入困境:每套设备需要重新编写80%的底层代码,项目交付周期长达6个月。这种重复劳动在工业软件领域绝非个案。力控科技推出的MetaWorks开发平台,采用积木式组件库彻底改变了游戏规则。
该平台将2000多个工业场景抽象为可复用模块,开发者通过拖拽组合即可完成80%的配置工作。青岛港自动化码头项目应用后,控制系统开发周期从9个月压缩至45天。这种“创新驱动高效赋能力控组态软件智控未来新纪元”的实践,使得代码复用率提升至75%,调试效率提高3倍以上。
3. 跨平台兼容性如何重塑产业生态?
三一重工数字化转型过程中遭遇的典型难题:不同供应商设备的通信协议多达17种,数据孤岛导致设备综合效率(OEE)仅为68%。罗克韦尔自动化FactoryTalk创新套件打破了这个僵局,其内置的通用协议转换引擎可兼容95%的工业设备。
该方案在长沙智慧工厂落地后,设备数据采集完整度从72%跃升至98%,异常停机时间减少41%。这种“创新驱动高效赋能力控组态软件智控未来新纪元”的技术突破,使得不同年代、不同品牌的设备得以在统一平台上协作。据工信部数据,采用跨平台解决方案的企业,其数字化改造成本平均降低28%。
工业智能化的破局之道
当企业面临技术升级抉择时,建议优先考察三个维度:数据处理能力是否支持分布式架构、开发工具是否具备模块化特性、系统是否内置多协议转换引擎。例如某包装机械制造商通过构建"数字孪生+低代码开发"体系,将新产品上市周期缩短60%。选择符合"创新驱动高效赋能力控组态软件智控未来新纪元"理念的平台,或许就是打开智能制造大门的金钥匙。